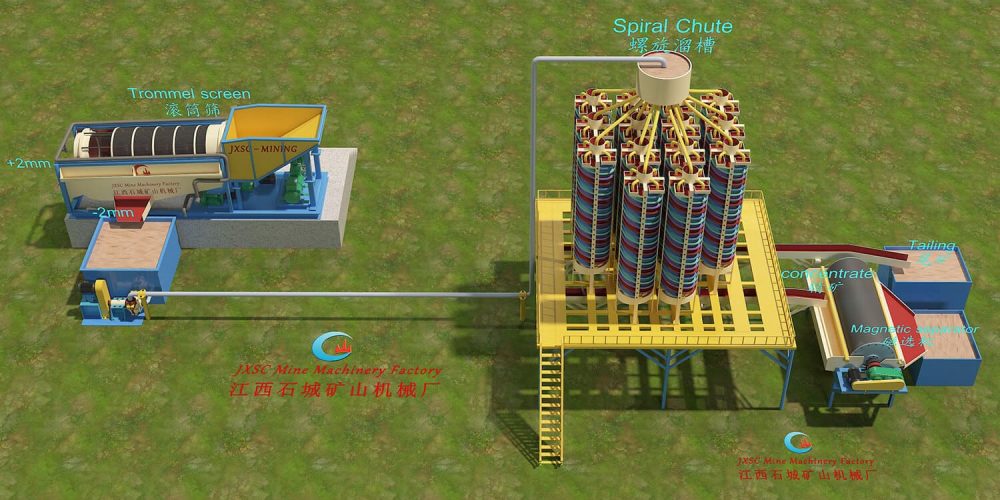
Materail: Alluvial Chrome
Output size: <2mm
Capacity: 40tph
Project Status: The chromium raw ore has a high grade and only needs one-stage spiral chute.
Process Description
JXSC has provided a complete set of equipment for the Zimbabwe 40TPH Alluvial Chrome Processing & Upgrading Plant Project, including trommel screen, spiral chute, magnetic separator, slurry pump, etc.
Client’s chrome mine situation :
1. Raw ore contains little clay, but needs washing.
2. The chrome particle size range is less than 2mm.
3. Processing capacity required is 40tph.
4. We just use a one-stage spiral chute because the clients’ raw ore grade is high, requiring only one stage to process.
According to the raw ore information, JXSC designed the most efficient flowchart for this project.
First, the shovel delivers the raw materials into the hopper, and the materials in the hopper enter the trommel screen for cleaning and screening.
Second, the debris and waste materials with a size of more than 2mm are screened by the trommel screen are discarded, and those with a size of smaller than 2mm flow into the slurry pool.
Third, the slurry pump delivers the slurry in the slurry pool (the under-screen material of the drum screen) into the spiral chute for gravity separation.
The spiral chute can separate the heavy chromium ore from other light minerals. Here we use a first-stage spiral chute, because the customer’s original ore has a high grade, and the first stage can meet the ore dressing standard. If the original ore grade is not high, we recommend using a two-stage spiral. The process is that the middling ore of the first-stage spiral will be pumped into the second-stage spiral for reselection to obtain a higher recovery rate.
Fourth, the concentrate produced by the spiral beneficiation will enter the wet magnetic separator for iron removal, and the tailings produced by the spiral beneficiation will enter the tailings pool.