High-sulfur bauxite, characterized by sulfur content exceeding the industrial threshold (typically >0.7%), poses significant challenges for alumina production. Sulfur impurities not only degrade product quality but also corrode equipment and emit harmful gases (e.g., SO₂) during processing. To address these issues, five mainstream desulfurization methods—roasting, flotation, bioleaching, high-pressure acid leaching (HPAL), and integrated processes—have been developed, each with distinct mechanisms and applicability. This article systematically analyzes these technologies, comparing their principles, processes, and industrial relevance to guide method selection for Bauxite with different sulfur forms.
5 Mainstream Desulfurization Methods for High-Sulfur Bauxite Ore
Desulfurization of high-sulfur bauxite is a complex industrial process that necessitates a comprehensive consideration of both technical feasibility and economic benefits. The following are 5 mainstream desulfurization methods and key technical points:
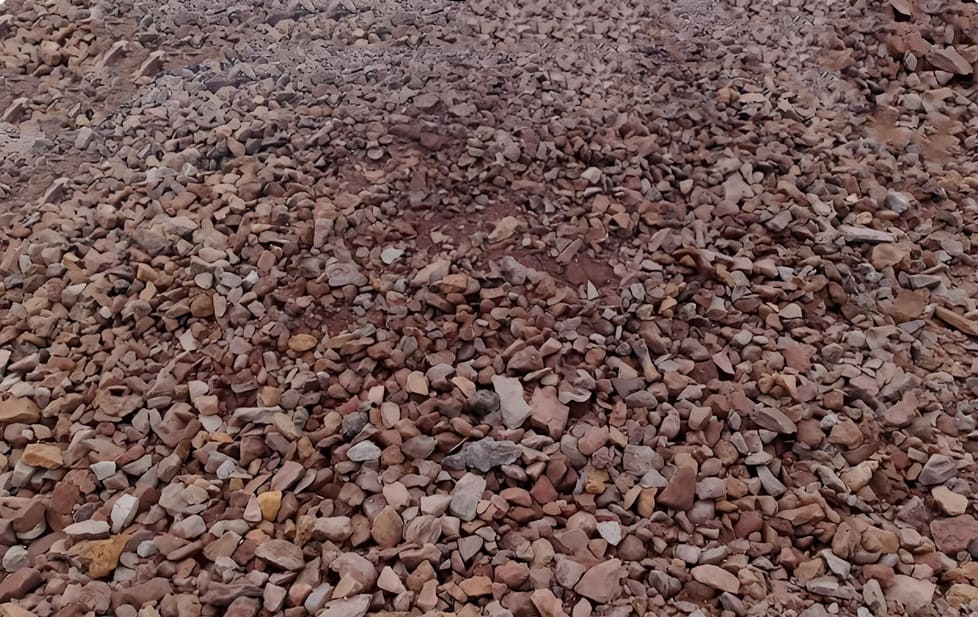
1. Roasting desulfurization method (most mature process)
- Operating temperature: 500-700℃ (medium temperature roasting)
- Core equipment: rotary kiln or boiling furnace
- Technical advantage: desulfurization rate can reach more than 85%
- Key control: precise temperature control to avoid phase transition from γ-Al₂O₃ to α-Al₂O₃
2. Flotation desulfurization method (suitable for high organic sulfur)
- Agent system: butyl xanthate + pine oil combination
- Process parameters: slurry pH value 8-9, concentration 30-35%
- Separation index: Concentrate sulfur content can be reduced to below 0.3%
- Innovation direction: electrochemical flotation technology research
3. Biological leaching method (green and environmentally friendly new process)
- Strain selection: acidophilic Thiobacillus (At.f strain)
- Leaching conditions: pH 1.5-2.5, temperature 30-35℃
- Cycle control: 7-15 days leaching cycle
- Supporting measures: the tail gas biofilter needs to be set up
4. High-pressure acid leaching method (high-efficiency deep desulfurization)
- Process parameters: 180-220℃, 2-3MPa pressure
- Acid consumption control: sulfuric acid dosage 20-30kg/t ore
- Technical difficulties: A titanium high-pressure reactor is required
- By-product: recoverable elemental sulfur
5. Combined process flow (complex ore treatment)
- Typical combination: flotation-roasting secondary desulfurization
- Economic indicators: comprehensive desulfurization cost reduction of 15-20%
- Innovation case: microwave-assisted roasting technology (desulfurization rate increased by 12%)
The following is a systematic analysis of the five mainstream desulfurization methods for high-sulfur bauxite, including technical principles, process flow, and feature comparison.
Roasting Desulfurization (Pyro-desulfurization)
Roasting desulfurization decomposes sulfur-containing minerals at high temperatures, and sulfur escapes as sulfur dioxide gas. For example, pyrite reacts with oxygen at high temperatures to produce ferric oxide and sulfur dioxide.
Technical Principles
- Thermal decomposition: FeS₂ → FeS + S(g)↑ (400-500°C)
- Oxidation: 4FeS + 7O₂ → 2Fe₂O₃ + 4SO₂↑ (>600°C)
- Sulfur phase transformation: Solid S → Gaseous SO₂ → Fixed as CaSO₄
Process Flow
Ore crushing (<3mm) → Drying (moisture <5%) → Rotary kiln roasting (three zones: drying at 300°C/reaction at 650°C/cooling at 200°C) → Cyclone dust removal → Alkali absorption (SO₂ recovery >95%) → Desulfurized concentrate (S <0.5%)
Key Features
- Advantages: Mature technology (used in 80% of domestic capacity), high throughput (single kiln: 3,000 t/d).
- Limitations: High energy consumption (35 kg standard coal/t), Al₂O₃ loss (3-5%).
- Innovations: Oxygen-enriched roasting (15% fuel reduction), microwave-assisted heating (40% shorter reaction time).
The advantages of high-sulfur bauxite roasting desulfurization are high desulfurization efficiency, short process, and the ability to remove organic interference. The disadvantages are that the long roasting time will increase costs, may affect the dissolution rate of alumina, require high energy consumption, and have high requirements for high-temperature resistance of equipment.
Flotation Desulfurization
The separation is achieved by utilizing the difference in surface properties between sulfide and oxide ores in the slurry. The sulfides (such as pyrite) in high-sulfur bauxite have different hydrophilicity from other mineral surfaces. After adding flotation reagents, the sulfides will attach to the bubbles and float out, separating from the bauxite.
Mechanism
- Xanthate adsorption: C₄H₉OCSS⁻ + FeS₂ → C₄H₉OCSS-FeS₂ (enhanced hydrophobicity).
- Froth flotation: Hydrophobic sulfur minerals rise with bubbles, while hydrophilic alumina remains.
Process Design
Grinding (75% -200 mesh) → Slurry conditioning (Na₂CO₃ adjusts pH to 8.5) → Roughing (80 g/t xanthate) → Three-stage cleaning → Tailings dewatering
Case Study: Processing ore with 2.8% S yields concentrate at 0.25% S and 92% Al₂O₃ recovery.
Technical Highlights
- Suitability: Less effective for finely disseminated sulfur (<10 μm).
- Cost: Reagent cost ~15 RMB/t ore.
- Advances: Electro-catalytic flotation (+8% recovery), nanobubble generators (20% energy savings).
The advantages of high-sulfur bauxite flotation desulfurization are a simple process, low cost, environmental protection, and comprehensive resource utilization. The disadvantages are high requirements on ore properties and precise control of reagent use.
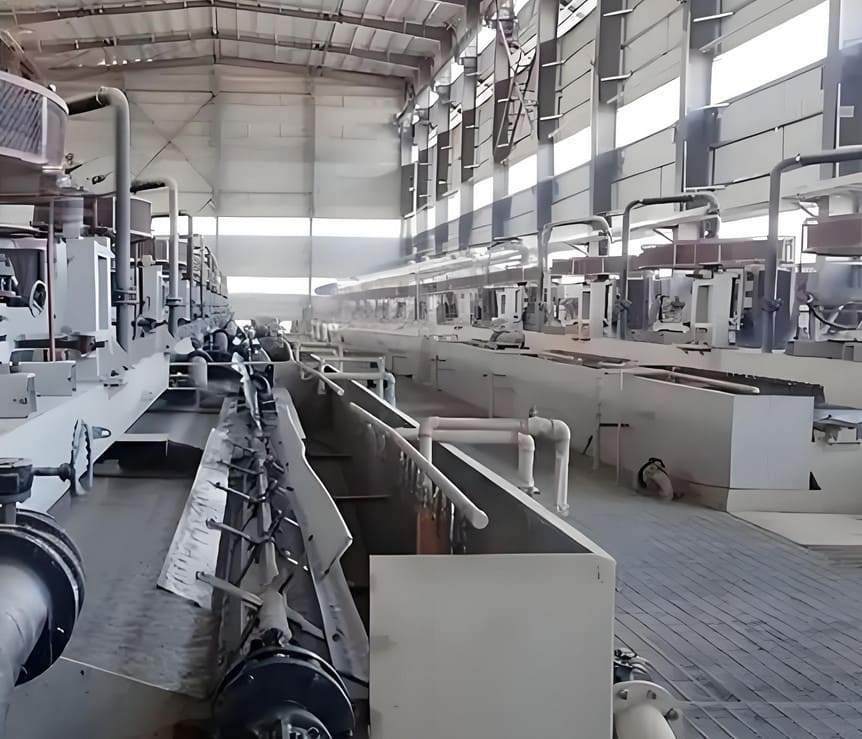
Bioleaching
Bioleaching desulfurization relies on the oxidation ability of microorganisms, such as Thiobacillus ferrooxidans, which can oxidize low-valent sulfur ions in pyrite into sulfate ions.
Biochemical Reactions
- Direct action: At.ferrooxidans oxidizes Fe²⁺ → Fe³⁺ (electron transfer)
- Indirect action: Fe³⁺ + FeS₂ → Fe²⁺ + S⁰ (cyclic oxidation)
- Sulfur metabolism: S⁰ → SO₄²⁻ (via sulfur-oxidizing bacteria)
Operational Flow
Bacteria culturing (OD₆₀₀ ≥0.8) → Heap leaching (4m height, 8 L/m²·h irrigation) → Leachate treatment (lime neutralization) → 21-day cycle
Parameters: ORP >450 mV, Fe³⁺/Fe²⁺ >10:1
Core Advantages
- Eco-friendly: Zero greenhouse gas emissions
- Low cost: Operating expenses at 1/3 of roasting
- Challenge: 50% efficiency drop in winter (northern regions)
The advantages of bioleaching desulfurization of high-sulfur bauxite are: low cost and energy consumption, and environmental protection. The disadvantages are that there are few studies, and there are problems such as difficulty in strain screening, high production conditions, difficult process control, long cycle, and unstable effect, which are far from market application.
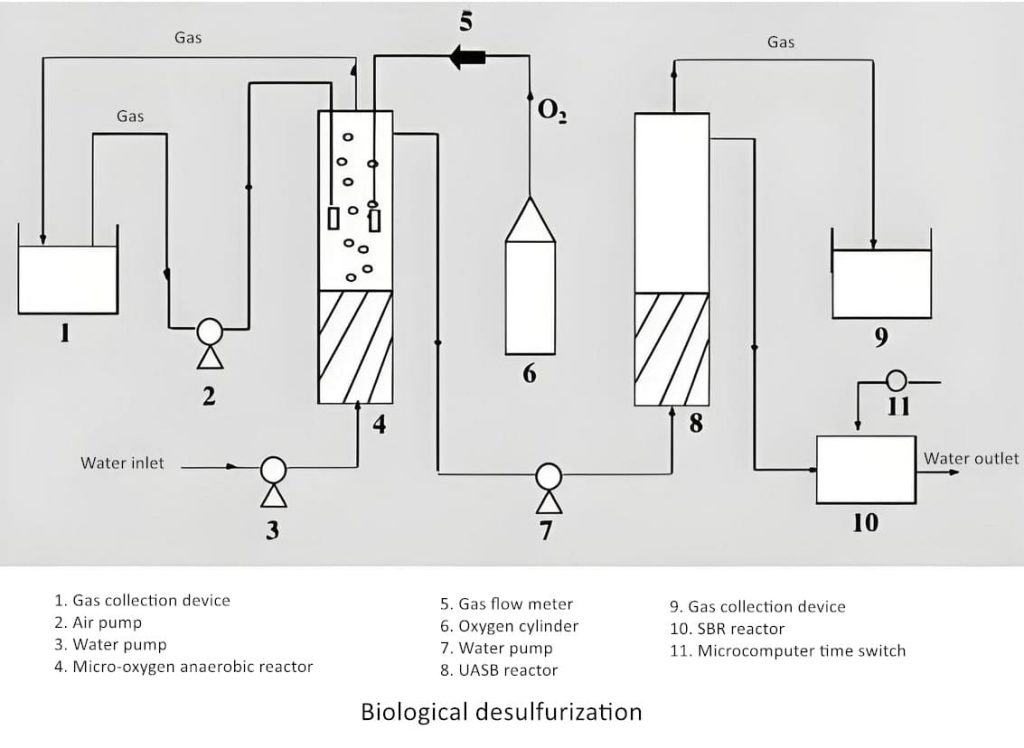
High-Pressure Acid Leaching (HPAL)
Reaction Kinetics
- Acid dissolution: FeS₂ + H₂SO₄ → FeSO₄ + H₂S↑ (160°C, Eₐ=85 kJ/mol)
- Oxidation: H₂S + 2O₂ → H₂SO₄ (under pressure)
System Components
Titanium autoclave (C276 lining) → Four-stage flash cooling → H₂S recovery (Claus process) → Iron removal (goethite process)
Typical conditions: Acid/ore ratio 1:2.5, O₂ partial pressure 0.8 MPa
Techno-Economics
- Ideal for high-sulfur ore (S >8%)
- High capex (>500 million RMB/line)
- Byproduct value: 30 kg sulfur/t ore
Combined (Integrated) Processes
Typical Combinations
- Option A (Refractory ore): Bio-preleaching (30% S removal) → Enhanced roasting (550°C) → Amine-based tail gas absorption.
- Option B (High organic S): Microwave activation (2450 MHz, 5 min) → Flotation → Residual S roasting.
Performance Comparison
Combination | Total S Removal | Al₂O₃ Loss | Energy Index |
Flotation-Roasting | 96% | 2.8% | 0.85 |
Bio-Leaching | 89% | 1.2% | 0.65 |
Case Study
A Guangxi plant adopted “fluidized roasting + selective flocculation,” reducing S from 4.7% to 0.15% while increasing Al₂O₃ recovery to 94.5% and cutting costs by 18%.
Techno-Economic Comparison
Method | Target S Form | Capex (RMB/t) | Opex (RMB/t) | Scale Applicability |
Roasting | Mixed S | 300-400 | 80-120 | >1 Mtpa |
Flotation | Liberated S | 150-200 | 25-40 | 0.3-1 Mtpa |
Bioleaching | Disseminated S | 80-100 | 15-30 | <0.5 Mtpa |
HPAL | Included S | 600-800 | 150-200 | >2 Mtpa |
Conclusion
The decarbonization-driven era demands cost-effective and environmentally sustainable desulfurization solutions for high-sulfur bauxite. While roasting dominates due to its technological maturity and scale of treatment, flotation performs better for monomer dissociative sulfur treatment; bioleaching offers a green alternative but is limited by climatic conditions and reaction rates; and high-pressure acid leaching is suitable for treating ultra-high-sulfur ores, despite its high investment cost. Emerging combination processes, such as bio-roasting, show higher alumina recovery and lower carbon footprints. In the future, technological breakthroughs such as low-temperature plasma and nanocatalysis may redefine the standard of desulfurization efficiency. When choosing a process, companies need to consider factors such as technical feasibility, operating costs and environmental and social impacts.