In the flotation process, the operating concept of “three cleanings and three scavengings” can indeed be called a “golden rule”. Its core slogan, “cleaning improves grade, scavenging ensures recovery,” succinctly summarizes the core idea of this concept. Following, we will discuss it in detail.
Grade VS Recovery
In the process of mineral flotation, Grade and Recovery are the two most important technical and economic indicators, which directly affect the benefits of the mineral processing plant.
Basic Definitions
Index | Formula | Unite | Meaning |
Grade | Mass of Valuable Mineral/Total Mass of Concentrate x100% | % | Purity of concentrate, determines the selling price |
Recovery | Mass of Valuable Mineral in Concentrate/Mass of Valuable Mineral in Feed ore x100% | % | Resource utilization rate, determines production and revenue |
Grade: refers to the percentage of the target valuable component in the concentrate. The higher the grade, the more “pure” the concentrate is and the higher its value is. Just like gold, a gold bar with 99.99% purity is naturally much more valuable than a gold bar with 90% purity.
Recovery: refers to the amount of valuable metal contained in the final concentrate as a percentage of the total amount of valuable metal in the original ore. The higher the recovery rate, the more treasures we “rescue” from the original ore and the fewer losses we suffer.
Relationship Between Them (Trade-off)
Ideal Target: High Grade + High Recovery
However, in practice, they typically exhibit an inverse relationship:
- Increasing Recovery(more froth scraping) → More impurities → Lower grade
- Increasing Grade(less froth scraping) → Some valuable minerals lost → Lower recovery
Grade and recovery rate are often a pair of contradictions. Just like sifting sand, if you want to get the most uniform and clean fine sand (high grade), you have to use a very fine sieve, but in this way, a lot of slightly coarser sand (still sand) will be sieved out as impurities, resulting in waste (low recovery rate). On the contrary, if you want to retain as much sand as possible (high recovery rate), you must use a coarser sieve; however, this will inevitably mix in some small stones and debris (low grade).
Key Influencing Factors
Factor | Impact on Grade | Impact on Recovery | Optimization Method |
Reagent Dosage | Excess → More impurities → ↓ Grade | Insufficient → Poor mineral adsorption → ↓ Recovery | Dynamic adjustment of collectors/inhibitors |
Froth Layer Thickness | Thin layer → High grade (less scraped impurities) | Thick layer → High recovery (more mineral collection) | Adjust scraper speed (±5cm optimal range) |
Number of Cleaning Stages | Each stage ↑ Grade by 2–5% | Each stage ↓ Recovery by 1–3% | Typically 2–3 cleaning stages (for copper) |
Grinding Fineness | Too fine → Slime contamination → ↓ Grade | Too coarse → Unliberated particles → ↓ Recovery | Control -200 mesh at 65–75% (copper example) |
How can we achieve both “purity” and “yield”? Mineral processing engineers have devised a smart solution – process division, where each unit performs its specific task. This is the essence of the “three-cleaning and three-scavenging” process.
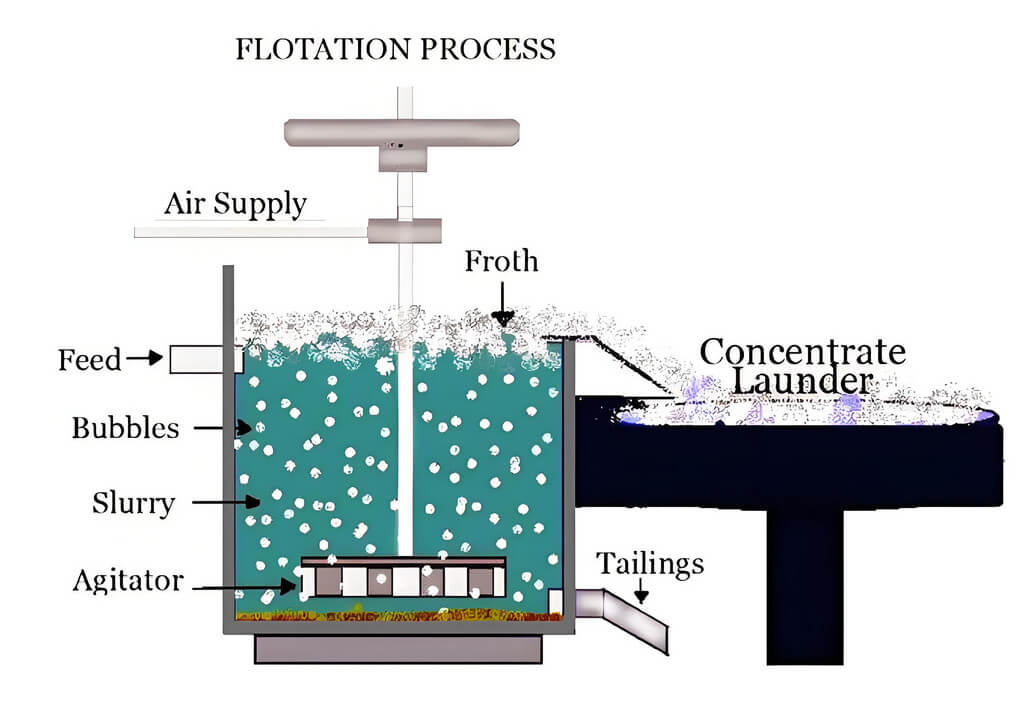
"Three Cleaning and Three Scavenging": A Combination Punch with Clear Division of Labor
As a classic flotation configuration, the “Three Cleanings, Three Scavengings” process divides flotation into three key stages: Roughing, Cleaning, and Scavenging, achieving optimal balance between grade and recovery.
Core Process Flow
Stage | Objective | Key Operation | Output Stream |
Roughing | Rapid bulk recovery (>80% target mineral) | High-intensity conditioning, bulk flotation | Rougher concentrate + Tails |
Cleaning (3x) | Upgrade grade (remove gangue) | Multi-stage re-flotation with regrinding (if needed) | Final concentrate + Middlings |
Scavenging (3x) | Maximize recovery from low-grade streams | Enhanced reagent dosage, longer retention time | Scavenger concentrate (returned to roughing) + Final tails |
Roughing
Roughing is the first stage, and the goal is to “better kill by mistake than let go”, and capture most of the valuable minerals from the original ore as much as possible to form “rough concentrate”. At this time, we are not too demanding about the grade, and the primary goal is to ensure that the valuable minerals are not thrown away as tailings too early.
Three Cleaning
Although the “rough concentrate” obtained from roughing is rich in valuable minerals, it is also mixed with a lot of “mistaken” gangue. In order to make the product purer, we need to “purify” it, which is called cleaning. The so-called “three cleanings” means that the rough concentrate is cleaned three times in a row.
First(Primary) Cleaning
The coarse concentrate is sent to the first group of flotation tanks. The goal is to remove a part of the gangue that is most likely to fall off. The resulting foam product enters the next step, and the remaining pulp (called “concentration middling”) is returned to the roughing system to avoid waste.
Secondary Cleaning
The foam product of the primary cleaning is sent to the second group of separation tanks for further purification.
Third Cleaning
The foam product of the secondary cleaning is purified for the third and final time.
Each time it passes through a cleaning, it is like filtering it with a finer sieve, and the grade of the concentrate goes up a level. The foam that finally comes out of the third cleaning is the high-grade final concentrate product we want. This process perfectly interprets “selection to improve grade” – its only goal is to sacrifice a small amount of recovery rate in exchange for maximizing product grade.
Three Scavenging
Now let’s look back at the roughing stage. Although most of the remaining slurry (roughing tailings) is waste rock, are there still some “slippery fish” that have not had time to float up or are not firmly attached? The answer is yes. If it is thrown away directly, it will be a huge loss. In order to “return the grains to the warehouse”, we need to “salvage” this part of the tailings, which is scavenging. The so-called “three scavengings” refers to scavenging the roughing tailings three times in succession.
First scavenging: send the roughing tailings to the first set of scavenging tanks, and use relatively strong reagents and operating conditions to try to “scavenge” the remaining valuable minerals.
Second scavenging: carry out another scavenging of the tailings left after the first scavenging.
Third scavenging: conduct the last “carpet search”.
Each time you go through a scavenging process, it’s like digging through the waste pile again, trying to pick up as much valuable stuff as possible. The foam product obtained by scavenging (lower grade, called “scavenging ore”) is usually returned to the roughing or previous process for reprocessing, and the slurry finally discharged after three scavenging processes is the final tailings that can be discarded. This process accurately reflects the “scavenging to ensure recovery” – its core mission is to do everything possible to “catch up” the lost valuable minerals regardless of grade, and ensure the total recovery rate.
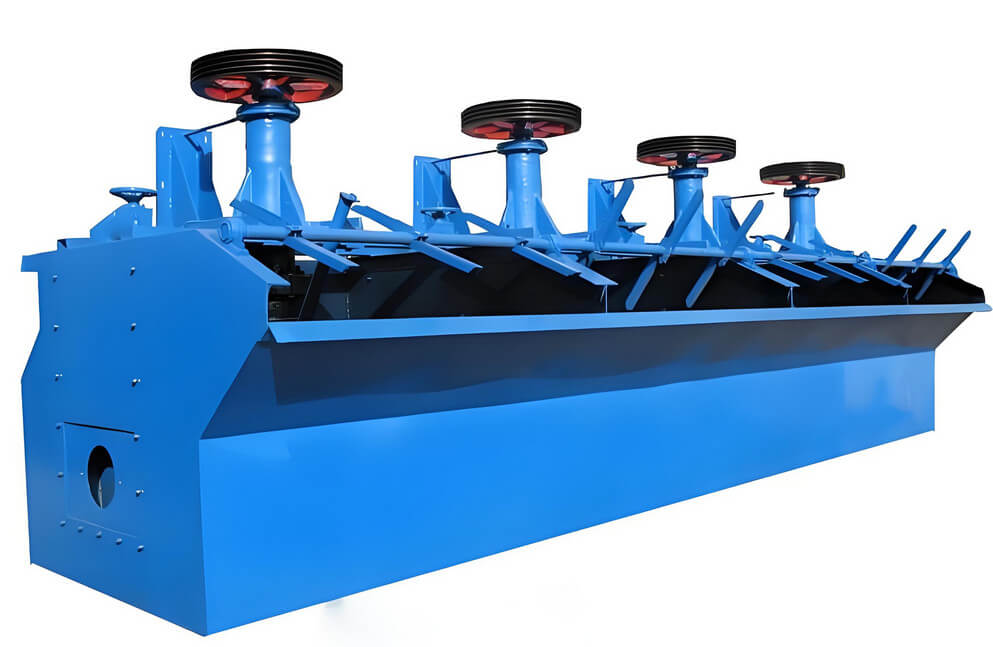
Cleaning & Scavenging
Cleaning improves grade, and scavenging ensures recovery. These ten words accurately summarize the core logic of multi-stage flotation process design and are a classic embodiment of system engineering thinking in the field of mineral processing. It is not a simple superposition of processes, but a subtle strategy for decoupling and optimizing complex systems.
In the mineral processing process, the “reciprocal relationship” between grade and recovery rate is an objective metallurgical limitation. It is difficult for a single flotation unit to achieve the optimal point of both indicators at the same time. The “three-cleaning and three-scavenging” process successfully solves this problem by building a closed-loop circulation system with a clear division of labor.
Cleaning stage: Its design goal is to maximize selectivity. Through step-by-step cleaning, the inclusions and inter-growth gangue minerals are systematically excluded, and the grade of the coarse concentrate is raised to commercial specifications. The “mid-ore” product of this stage, that is, the material with a grade between the concentrate and the tailings, is returned to the previous operation, ensuring the internal circulation of valuable minerals and avoiding direct losses in the pursuit of high grade.
Scavenging stage: Its design goal is to maximize the recovery rate. By strengthening the reagent system and operating conditions, the valuable minerals with slow flotation dynamics or in a depleted state in the roughing tailings are recovered to the extreme. The product (sweeping and scavenging ore) has a low grade, but because it is sent back to the front end of the process for reprocessing, it realizes the “closed-loop recovery” of valuable metals and ensures that the final discarded tailings reach the lowest economically acceptable grade.
Therefore, the essence of “three cleanings and three scavengings” is to decompose a complex dual-objective optimization problem into two relatively independent single-objective optimization subsystems. This modular process design not only greatly improves the robustness and controllability of the entire mineral processing system, but also makes it possible to fine-tune the properties of different ores, and finally achieves the optimization of overall metallurgical performance and economic benefits under specific technical and economic conditions.