Gold mining plays a significant role in Tanzania’s economy, contributing to employment and foreign exchange earnings. Among the various gold extraction methods, the Carbon-in-Leach (CIL) process has proven effective for processing oxide and sulfide ores. This article details a 200-ton-per-day (t/d) Carbon-in-Leach (CIL) processing plant tailored for oxidized gold ore, showcasing its cutting-edge efficiency, superior recovery rates(gold recovery rate exceeding 92%), and environmental sustainability. It becomes a model for oxide ore development in East Africa. This article will deeply analyze the process flow, technical highlights, and operational results of the project.
200 TPD Gold CIL Processing Plant
Project Overview
The mining area is located in the gold mineralization belt of Tanzania. The ore is mainly oxidized ore. The gold occurrence state is complex, with high mud content and a small amount of sulfide.
Customer requirements:
- The designed daily processing capacity is 200 tons, which is suitable for the characteristics of high-clay oxidized ore.
- Environmental protection compliance, in line with local strict emission standards.
- Shorten the construction period and control investment costs.
Gold CIL Process Design
According to the characteristics of the ore, the “crushing-grinding-leaching-adsorption-desorption electrolysis” full-process CIL process is adopted to achieve efficient gold recovery. The process is as below:
Crushing and Grinding System
Gentle Liberation for Oxide Ores, unlike sulfide ores, oxidized gold requires minimal crushing aggression to avoid sliming (important for clay-rich ores).
Two-stage crushing (Jaw Crusher + Cone Crusher)
- Coarse crushing: jaw crusher (feed particle size ≤400mm → ≤75mm).
- Fine crushing: cone crusher + vibrating screen closed-circuit circulation, ensuring that the particle size of the mill is ≤
- Optional screen to ensure uniform feed size.
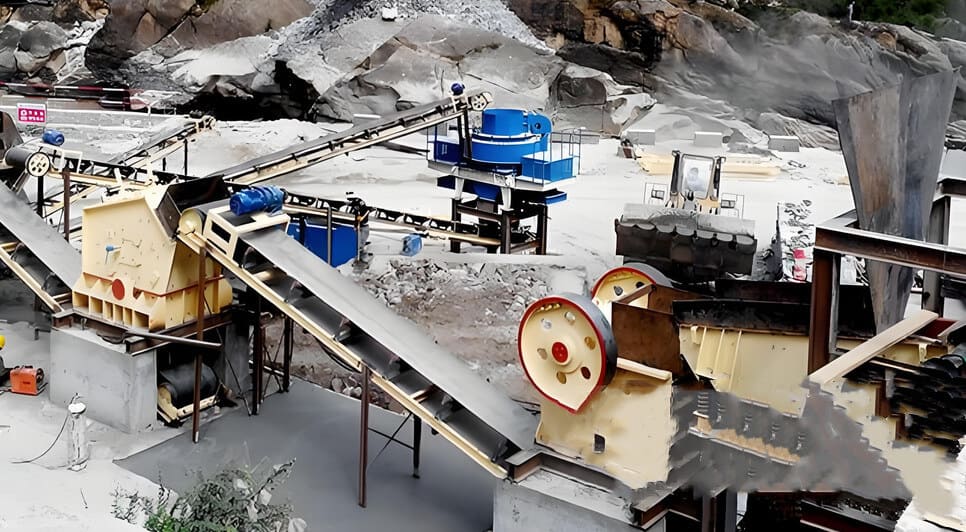
Grinding and classification
- Wet grid ball mill + spiral classifier, grinding fineness reaches -200 mesh (75µm) accounting for 85%.
- Add dispersant to solve the mud encapsulation problem and improve the gold leaching rate.
CIL Leaching And Adsorption System
After grinding, slurry flows into leaching tanks, and the CIL plant is streamlined for oxidized ore’s rapid leaching.
- 7-stage series leaching tank (first 2 stages pre-leaching, last 5 stages CIL), total residence time 36 hours.
- Activated carbon countercurrent adsorption, gold-carrying carbon grade reaches 3000g/t.
- Cyanide concentration 0.05%, pH value 10.5-11.5, precise reagent control.
Desorption Electrolysis And Smelting
- High temperature and high-pressure desorption process, desorption rate >98%.
- Electrolytic deposition to obtain gold mud, smelting to produce gold ingots with a purity of 99.5%.
Key Equipment List
Stage | Equipment | Function |
Crushing | Jaw crusher, cone crusher | Primary & secondary size reduction |
Grinding | Ball mill, hydrocyclone | Grind ore to fine slurry |
Leaching | Agitation tanks, carbon screens | Gold dissolution & adsorption |
Gold Recovery | Desorption column, electrowinning | Strip & precipitate gold from carbon |
Smelting | Induction furnace | Produce gold bars (Doré) |
Technical Highlights
Efficient pretreatment process
- Add a washing screen to remove clay and avoid clogging of the grinding system.
- Cyclone classification + thickener dehydration to optimize pulp concentration to 40-45%.
Energy-saving and consumption-reducing design
- The ball mill adopts variable frequency control to reduce energy consumption by 15%.
- Tailing dry discharge system achieves a water resource recycling rate of >85%.
Intelligent control system
- Full process DCS automatic control, real-time monitoring of key parameters.
- Online adjustment of ORP value in the leaching section to ensure leaching stability.
Environmental Protection & Sustainability
- Zero-emission treatment: Tailings are filtered and dry-stacked, and the filtrate is reused in the production process.
- Hazardous waste management: Cyanide detoxification system ensures that wastewater meets discharge standards.
- Community win-win: Local employees account for more than 60% of the total, and supporting public welfare facilities are built.
Project Achievements
Indicators | Data | Industry Average |
Daily Processing Capacity | 200t/d | 150-200t/d |
Gold Recovery Rate | 92.3% | 85-90% |
Construction Period | 12 months | 14-18 months |
Comprehensive Cost per Ton of Ore | $22.5/t | $25-28/t |
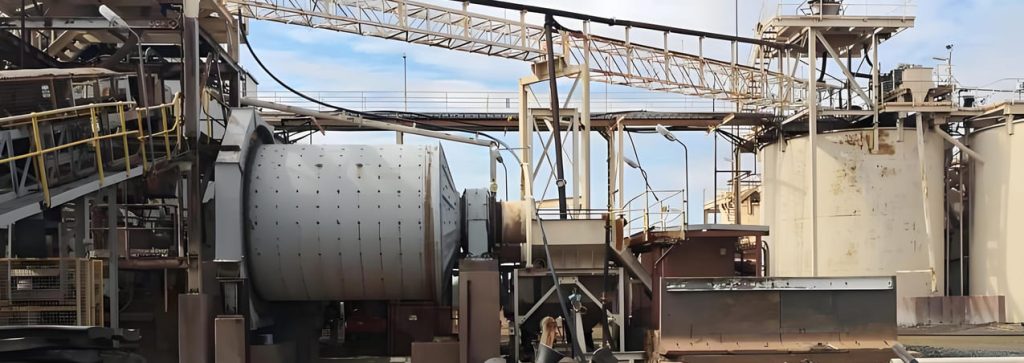
Why This Tanzania Gold Plant Prefer CIL Processing?
Carbon-in-Leach (CIL) is the most widely adopted process for extracting gold from oxidized ores due to its superior recovery, operational simplicity, and cost-effectiveness. Unlike refractory ores that require pre-treatment, oxidized gold ores contain freely liberated gold, making them ideally suited for direct cyanidation in a CIL plant. We will discuss why Tanzania oxidized gold uses CIL to process the gold.
1. Geological Suitability
Tanzania’s oxidized gold deposits (notably in Lake Victoria Goldfields and Geita Greenstone Belt) exhibit ideal CIL characteristics:
(1) Gold Liberation Superiority
- Surface-weathered free gold(80-95% liberation at 75μm grind size)
- Minimal sulfide content(<5% pyrite vs >30% in refractory ores)
- Lower preg-robbing carbon(0.1-0.3% vs 1-3% in carbonaceous ores)
(2) Mineralogical Advantages
Feature | Tanzanian Oxidized Ore | Refractory Ore |
Gold Carriers | Quartz/iron oxides | Sulfides |
Clay Content | Moderate (5-15%) | Low (<5%) |
Cyanide Soluble | >90% | <40% |
Crush Work Index | 8-12 kWh/t | 14-18 kWh/t |
2. Technical Advantages
(1) Capital Efficiency
- 30-40% lower CAPEX than flotation circuits
- Compact footprint(50% smaller than CIP)
- Simpler operation(4-6 staff per shift vs 8-10 for BIOX)
(2) Metallurgical Performance
Superior Gold Recovery (90–98%)
Oxidized gold ores dissolve readily in cyanide, allowing CIL to maximize extraction through:
- Simultaneous leaching & adsorption– Gold is continuously adsorbed onto activated carbon, preventing re-precipitation.
- Higher retention efficiency– By introducing carbon early, CIL recovers 5–10% more gold than Carbon-in-Pulp (CIP).
- Optimized cyanide consumption– Prevents excessive cyanide degradation from preg-robbing minerals.
Faster kinetics:
- 18hr leach time (vs 24+hrs for sulfide ores)
- Carbon loading 3000-6000g/t(2X CIP efficiency)
3. Why Other Methods Underperform Compared to CIL?
Method | Key Limitations for Oxidized Ores |
Heap Leaching | Low recovery (60–75%), slow kinetics, only viable for <2 g/t ores |
CIP | Lower gold recovery due to delayed carbon introduction |
Flotation | Unnecessary for liberated gold, adds costs for fine grinding & reagents |
Gravity Separation | Incomplete recovery (30–60%), requires additional cyanidation |
For oxidized gold ores, CIL offers the best balance of efficiency, cost, and simplicity, making it the industry-standard beneficiation method. The CIL production line provides a replicable solution for the development of similar oxidized mines in Tanzania and Africa because of its high process suitability and fast return on investment. We provide a “one-stop service” from beneficiation test, and engineering design to operation support to help global clients to explore Africa!