Zimbabwe is an important chrome ore resource country in the world. Its laterite chrome ore reserves are rich, but the beneficiation is difficult. In recent years, with the continuous advancement of beneficiation technology, the development and utilization of Zimbabwe’s laterite chrome ore have made significant progress. This article will provide a comprehensive analysis of the beneficiation technology for Zimbabwe’s laterite chrome ore, revealing the technical secrets behind the high recovery rate.
Ore Characteristics: the basis of mineral processing technology
Zimbabwe’s laterite chrome ore has unique mineralogical characteristics. The chromium in the ore mainly exists in the form of chromite, with fine embedded particles and an average particle size between 0.01-0.05 mm. The Cr2O3 content in the ore is generally 20-35%, but it also contains high amounts of magnesium oxide (10-15%) and aluminum oxide (15-25%), which increases the difficulty of mineral processing.
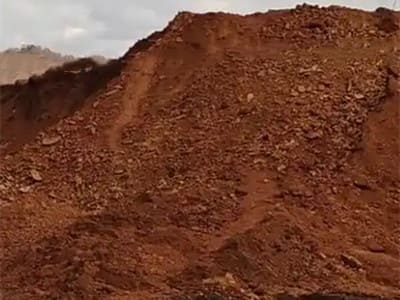
The physical properties of the ore are complex, with a density between 3.2-3.8g/cm³ and weak magnetism. Lateritization causes the ore structure to be loose and easy to mud, which puts special requirements on the mineral processing technology. A full understanding of these characteristics is the basis for formulating a reasonable mineral processing plan.
Crushing and Grinding: key technological breakthroughs
Given that laterite chrome ore is prone to being muddy, the process route of “more crushing and less grinding” is adopted. The jaw crusher is used for coarse crushing, and the high-pressure roller mill is used for medium crushing. The ore is crushed to -3mm, accounting for more than 90%. The grinding process employs a two-stage closed-circuit system, where the first stage utilizes a rod mill for coarse grinding and the second stage utilizes a ball mill for fine grinding.
Dispersants are added during the grinding process to control the slurry concentration at 60-65%, effectively preventing over-grinding and muddying. The hydrocyclone is used for classification to ensure that the -0.074mm particle content in the grinding product is controlled at 65-70%, creating good conditions for subsequent selection.
Separation Process: the key to efficient recovery
The combined process of “gravity separation-magnetic separation-flotation” is adopted. First, a spiral chute is used for rough separation, and the recovery rate can reach more than 70%. Then, a high-gradient magnetic separator is used for fine separation, and the magnetic field strength is controlled at 1.0-1.2T, which can effectively separate weakly magnetic minerals.
The flotation adopts a new collector CY-12, combined with the adjusting agent water glass, and reverse flotation is carried out under the condition of pH=8-9. The concentrate grade can be increased to more than 48%, and the recovery rate can reach more than 85%. The Cr2O3 content in the tailings is reduced to less than 2%, which greatly improves the resource utilization rate.
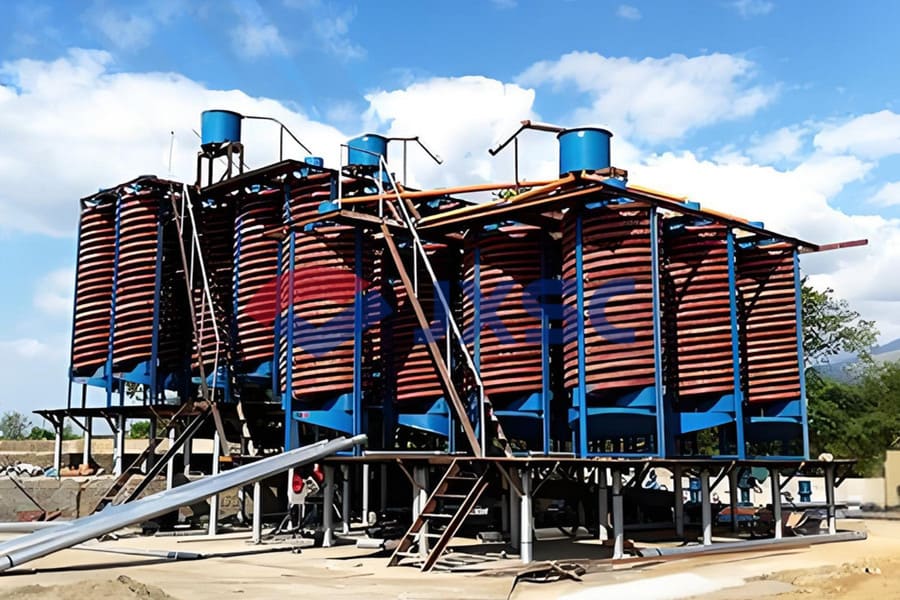
Dehydration and Drying: ensure product quality
The dehydration of concentrate adopts a combination process of a high-efficiency concentrator + filter press. The underflow concentration of the concentrator is controlled at 55-60%, and the moisture content of the filter cake of the filter press is controlled below 12%. The tailings are treated by a deep cone concentrator, and the underflow concentration reaches more than 65%, which is convenient for the storage of tailings ponds.
The concentrate is dried using a rotary dryer, and the hot air temperature is controlled at 300-350℃ to ensure that the product’s moisture content is less than 2%. The drying system is equipped with a dust removal device, and the dust emission concentration is less than 30mg/m³, meeting environmental protection requirements.
Technological Innovation: promote industry development
In recent years, Zimbabwe’s laterite chrome ore dressing technology has made many innovative breakthroughs. The development of new and efficient collectors has increased the concentrate grade by 3-5 percentage points; the application of high-pressure roller mills has reduced energy consumption by 30%; the introduction of automated control systems has increased production efficiency by more than 20%.
These technological innovations not only improve resource utilization but also greatly reduce production costs. According to statistics, after adopting the new technology, the processing cost per ton of ore is reduced by 15-20%, and the economic benefits are significantly improved.
Environmental Considerations and Sustainable Development
Modern processing plants in Zimbabwe incorporate comprehensive environmental protection measures. Dust collection systems cover all material transfer points, while water recycling rates exceed 85%. The implementation of dry stacking technology for tailings management significantly reduces the environmental footprint compared to conventional slurry disposal methods.
Future Development Trends
The Zimbabwean chrome industry is focusing on several key development areas:
- Development of more selective collectors to further improve concentrate quality
- Optimization of grinding circuits to reduce energy consumption
- Implementation of sensor-based ore sorting technologies for pre-concentration
- Advancement of bio-hydrometallurgical processing methods
- Integration of digital twin technology for process optimization
These technological directions promise to further enhance processing efficiency while reducing environmental impact and operational costs.
Economic Impact and Market Considerations
Zimbabwe’s chrome beneficiation advancements have substantially increased the country’s competitiveness in global markets. The ability to produce high-grade concentrates (48 %+ Cr₂O₃) has opened new market opportunities, particularly in the metallurgical industry, where premium prices are commanded for high-grade products. Local beneficiation has also created significant employment opportunities and promoted the development of downstream industries.
Comparative Analysis with Other Chrome-Producing Regions
While South Africa remains the global leader in chrome production, Zimbabwe’s technological advancements position it as a strong competitor, particularly in the production of high-grade concentrates from difficult-to-process lateritic ores. The country’s processing techniques now rival those employed in Kazakhstan and Turkey, traditionally known for their advanced chrome beneficiation capabilities.
Challenges and Opportunities
Despite these advancements, the Zimbabwean chrome industry faces several challenges:
- Infrastructure limitations, including power supply reliability
- Capital constraints for large-scale technological upgrades
- Regulatory complexities in mining and export policies
- Global market price volatility
- Need for continuous skills development
However, these challenges present opportunities for international collaboration, technology transfer, and investment partnerships that could further enhance the country’s position in the global chrome market.
Conclusion
Zimbabwe’s lateritic chrome beneficiation technologies have undergone a remarkable transformation, positioning the country as a technologically advanced producer in the global chrome industry. Through continuous innovation in mineral processing techniques, environmental management, and process optimization, Zimbabwe has successfully unlocked the economic potential of its challenging lateritic chrome resources. The ongoing development and implementation of cutting-edge processing technologies promise to further consolidate Zimbabwe’s position as a key player in the global chrome market while contributing to sustainable resource utilization and economic development.